Copper to Aluminium Busbar: A Comprehensive Guide
Delve deeply into every aspect of copper to aluminium busbars, exploring their definitions, applications, benefits, challenges, best practices for installation and maintenance, and future trends.
The transition from copper to aluminium busbars is a pivotal topic in modern electrical engineering, especially as industries increasingly seek cost-effective and lightweight alternatives without sacrificing conductivity and reliability. Busbars play an essential role in power distribution systems, acting as conductive pathways that efficiently carry electrical currents. In this comprehensive guide, we will delve deeply into every aspect of copper to aluminium busbars, exploring their definitions, applications, benefits, challenges, best practices for installation and maintenance, and future trends.
What are Busbars? An In-Depth Overview
Busbars are metallic strips or bars made of conductive materials such as copper or aluminium. They are utilized in power distribution systems to conduct substantial currents of electricity. Unlike wires or cables, busbars provide low impedance, allowing for efficient power transfer with minimal resistance. They are integral components in switchgear, electrical panels, and power distribution systems, ensuring safe and effective current flow.
Key Functions of Busbars:
- Current Distribution: Busbars distribute electrical power to various circuits within a system, maintaining uniform voltage across multiple points.
- Connection Points: They serve as central points for connecting multiple incoming and outgoing electrical circuits.
- Fault Protection: By providing a centralized path for current, busbars minimize the risk of overheating and short circuits.
Why Transition to Aluminium Busbars? A Detailed Analysis
The shift from copper to aluminium busbars is driven by several compelling factors:
Cost Efficiency:
Aluminium is significantly less expensive than copper, making it an economically viable option for large-scale installations. The cost per kilogram of aluminium is approximately 30-40% of copper’s cost, allowing industries to achieve substantial savings in material costs.
Lightweight Design:
Aluminium is approximately one-third the weight of copper, which reduces the overall structural load. This lighter weight facilitates easier handling during installation, lowers transportation costs, and reduces the mechanical stress on support structures.
Corrosion Resistance:
Modern aluminium busbars are manufactured with advanced surface treatments to resist oxidation and corrosion. Anodizing and coating techniques create a protective layer, preventing the formation of oxides and ensuring long-term conductivity.
Environmental Sustainability:
Aluminium is more abundant in the Earth’s crust and easier to recycle than copper. The recycling process for aluminium requires only 5% of the energy needed to produce new aluminium, significantly reducing its environmental footprint.
Challenges in Transitioning to Aluminium Busbars
While the benefits of aluminium are notable, the transition from copper to aluminium busbars is not without challenges:
Conductivity Differences:
Aluminium’s electrical conductivity is approximately 61% of copper’s, requiring larger cross-sectional areas to maintain the same current-carrying capacity. This necessitates careful design and sizing to prevent overheating and voltage drops.
Thermal Expansion:
Aluminium has a higher coefficient of thermal expansion than copper. Under high temperatures, aluminium expands more, increasing the risk of loosening connections. Engineers must use specific connection techniques to accommodate this expansion and maintain stable contact points.
Oxidation and Contact Resistance:
Aluminium is more susceptible to oxidation than copper. Aluminium oxide is non-conductive, potentially increasing contact resistance and reducing overall efficiency. To mitigate this, connectors and contact surfaces are treated with anti-oxidation compounds and mechanical cleaning methods.
Ensuring Reliable Connections: Copper to Aluminium Transition Joints
Creating secure, reliable connections between copper and aluminium busbars requires specialized techniques and materials to prevent galvanic corrosion and maintain electrical continuity.
Bimetallic Connectors:
Bimetallic connectors are designed to join dissimilar metals without causing galvanic corrosion. They consist of a copper-aluminium interface that prevents direct contact, minimizing the risk of electrochemical reactions.
Compression Joints:
Compression connectors are used to establish firm contact between busbars. Proper torque application ensures optimal surface contact and reduces resistance.
Surface Preparation and Treatment:
Before joining copper and aluminium, surfaces must be meticulously cleaned to remove oxides and debris. Anti-oxidation compounds are then applied to prevent future corrosion and enhance conductivity.
Best Practices for Installation
Accurate Sizing and Selection:
Aluminium busbars must be sized appropriately to handle the same current as copper. This typically involves increasing the cross-sectional area to compensate for aluminium’s lower conductivity.
Temperature Monitoring Systems:
Installing temperature monitoring sensors at connection points allows for real-time tracking of thermal performance, preventing overheating and ensuring operational safety.
Regular Maintenance and Inspections:
Conduct periodic inspections to identify signs of oxidation, corrosion, and thermal expansion. Re-tighten connections and reapply anti-oxidation compounds as necessary to maintain optimal performance.
Applications of Copper to Aluminium Busbars
Copper to aluminium busbars are widely used in various industries, including:
- Electrical Panels and Switchgear: Aluminium busbars are commonly used in power distribution panels to minimize costs and reduce weight.
- Renewable Energy Systems: Solar power installations employ aluminium busbars to transfer power efficiently while maintaining a lightweight infrastructure.
- Industrial Power Networks: Manufacturing facilities utilize aluminium busbars to transmit high currents in compact, modular configurations.
- Data Centers and Telecommunications: Aluminium busbars provide reliable power distribution for servers and network equipment, optimizing space and cost.
Conclusion
The transition from copper to aluminium busbars is a complex yet advantageous shift in power distribution systems. By understanding the distinct properties of both metals and employing proper connection techniques, industries can effectively harness the cost and weight benefits of aluminium while maintaining electrical performance. Through strategic design, careful installation, and consistent maintenance, aluminium busbars can offer a viable and sustainable alternative to copper in modern electrical infrastructure.
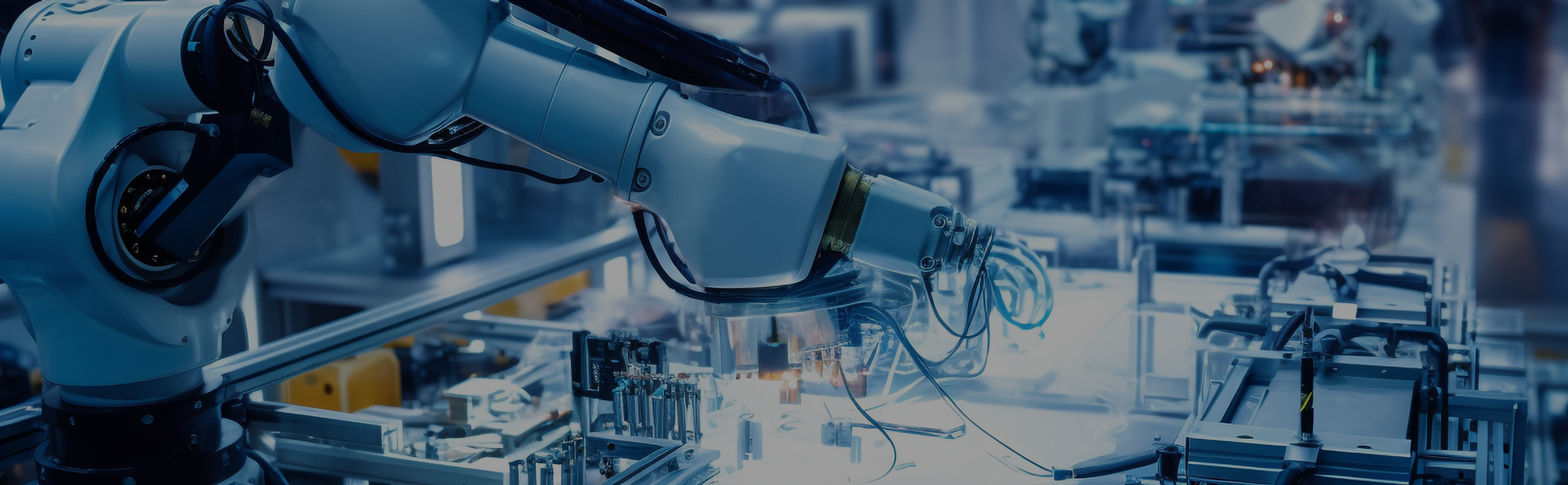